Blast furnace
|
Read other articles:

2022 song by KSI Not Over YetSingle by KSI featuring Tom GrennanReleased5 August 2022Genre Electronic drum and bass dance-pop[1] Length2:35Label Warner Atlantic Songwriter(s) Olajide Olatunji Richard Boardman Nick Gale Sam Brennan Sara Boe Tom Grennan Tom Hollings Producer(s) Digital Farm Animals Billen Ted KSI singles chronology Locked Out (2022) Not Over Yet (2022) Summer Is Over (2022) Tom Grennan singles chronology All These Nights(2022) Not Over Yet(2022) Lionheart (Fearl...

Ilustrasi Antasan Antasan adalah suatu istilah yang dipakai oleh Suku Banjar untuk menamai sistem perairan kanal mereka. Antasan merupakan suatu fenomena geomorfologi yang memperlihatkan keberlanjutan dan saling keterkaitan antara sungai-sungai kecil dengan sungai-sungai besar. Meskipun memiliki karakteristik sebagai saluran sekunder, antasan memegang peran yang lebih signifikan dalam sistem hidrologi.[1] Fungsi Fungsi utama antasan adalah sebagai jalur lalu lintas air yang menghubung...
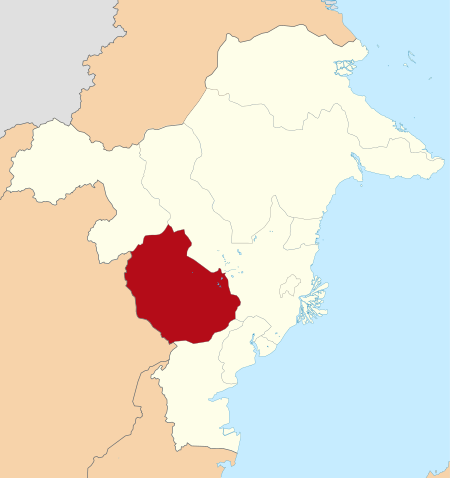
Peta lokasi Kabupaten Kutai Barat Berikut adalah daftar kecamatan dan kampung/kelurahan di Kabupaten Kutai Barat, Provinsi Kalimantan Timur, Indonesia. Kabupaten Kutai Barat terdiri dari 16 kecamatan, 4 kelurahan, dan 190 kampung. Pada tahun 2017, jumlah penduduknya mencapai 158.560 jiwa dengan luas wilayah 20.381,59 km² dan sebaran penduduk 8 jiwa/km².[1][2] Daftar kecamatan dan kampung/kelurahan di Kabupaten Kutai Barat, adalah sebagai berikut: Kode Kemendagri Kecamatan Ju...

Member states of the Swiss Confederation For Districts within each Swiss Canton, see Districts of Switzerland. Swiss cantons Schweizer Kantone (German) Cantons suisses (French) Cantoni svizzeri (Italian) Chantuns svizras (Romansh)Also known as:Stände, États, Stati Valais Ticino Grisons Geneva Vaud Neuchâtel Jura Bern Thurgau Zürich Aargau Lucerne Solothurn Basel-Landschaft Schaffhausen Uri Schwyz Glarus St. Gallen Appenzell Innerrhoden Appenzell Ausserrhoden Obwalden N...
School of medieval philosophy Averroes depicted in a painting by Italian artist Andrea di Bonaiuto. Florence, 14th century. Averroism refers to a school of medieval philosophy based on the application of the works of 12th-century Andalusian philosopher Averroes, (known in his time in Arabic as ابن رشد, ibn Rushd, 1126–1198) a commentator on Aristotle, in 13th-century Latin Christian scholasticism. Latin translations of Averroes' work became widely available at the universities which w...

Bibisan Ostorhinchus aureus Status konservasiRisiko rendahIUCN193332 TaksonomiKerajaanAnimaliaFilumChordataKelasActinopteriOrdoKurtiformesFamiliApogonidaeGenusOstorhinchusSpesiesOstorhinchus aureus Tata namaSinonim taksonApogon aureus (en) lbs Bibisan ( Ostorhinchus aureus ) adalah spesies ikan yang tersebar luas dalam famili Apogonidae yang ditemukan di Laut Merah dan lepas Afrika Timur hingga Papua Nugini, utara hingga Jepang, dan selatan hingga Australia . Keterangan Ikan ini berwarna temb...

This article needs additional citations for verification. Please help improve this article by adding citations to reliable sources. Unsourced material may be challenged and removed.Find sources: Sami Solh – news · newspapers · books · scholar · JSTOR (February 2018) (Learn how and when to remove this template message) Sami Solhسامي الصلح3rd Prime Minister of LebanonIn office23 August 1945 – 22 May 1946PresidentBishara Al KhouriPrece...

Study with uncontrolled variable of interest Anthropological survey paper from 1961 by Juhan Aul (et) from University of Tartu who measured about 50 000 people In fields such as epidemiology, social sciences, psychology and statistics, an observational study draws inferences from a sample to a population where the independent variable is not under the control of the researcher because of ethical concerns or logistical constraints. One common observational study is about the possible effe...

العلاقات التشيكية الغينية التشيك غينيا التشيك غينيا تعديل مصدري - تعديل العلاقات التشيكية الغينية هي العلاقات الثنائية التي تجمع بين التشيك وغينيا.[1][2][3][4][5] مقارنة بين البلدين هذه مقارنة عامة ومرجعية للدولتين: وجه المقارنة التشيك غي...

Swiss cyclist Florian VogelVogel in the UCI MTB World Cup race in La Bresse (2012)Personal informationFull nameFlorian VogelBorn (1982-02-18) 18 February 1982 (age 42)Aarau, SwitzerlandTeam informationDisciplineMountain bike racingRoleRiderRider typeCross-country Medal record Men's mountain bike racing Representing Switzerland World Championships 2006 Rotorua Team cross-country 2007 Fort William Team cross-country 2000 Sierra Nevada Team cross-country 2004 Les Gets Team c...

American producer, writer and director (born 1956) John WellsWells in 2012BornJohn Marcum Wells (1956-05-28) May 28, 1956 (age 67)Alexandria, Virginia, U.S.EducationCarnegie Mellon University (BFA) University of Southern California (MFA)Occupation(s)Producer, writer, directorYears active1987–present John Marcum Wells (born May 28, 1956) is an American producer, writer, and director. He is best known for his role as showrunner and executive producer of the television series ER, Thi...

André Dias André Dias nel 2010 con la maglia del San Paolo Nazionalità Brasile Altezza 184 cm Peso 80 kg Calcio Ruolo Difensore Termine carriera 1º luglio 2014 Carriera Giovanili 199?-1998 Pales. de São Bernardo Squadre di club1 1998-2001 Paraná37 (2)2002 Flamengo11 (0)2003 Paysandu26 (1)2004-2005 Goiás74 (3)2006-2009 San Paolo109 (6)2010-2014 Lazio111 (5) 1 I due numeri indicano le presenze e le reti segnate, per le sole partite di campionato....

Danish lawyer, botanist and politician (1789–1852) Joakim Frederik SchouwC. A: Jensen: J. F. Schouw, 1836Born(1789-02-07)7 February 1789Copenhagen, DenmarkDied28 April 1852(1852-04-28) (aged 63)Copenhagen, DenmarkNationalityDanishAlma materUniversity of CopenhagenScientific careerFieldsLawyer, botanist Joakim Frederik Schouw (7 February 1789 – 28 April 1852) was a Danish lawyer, botanist and politician. From 1821, professor in botany at the University of Copenhagen — first ext...

追晉陸軍二級上將趙家驤將軍个人资料出生1910年 大清河南省衛輝府汲縣逝世1958年8月23日(1958歲—08—23)(47—48歲) † 中華民國福建省金門縣国籍 中華民國政党 中國國民黨获奖 青天白日勳章(追贈)军事背景效忠 中華民國服役 國民革命軍 中華民國陸軍服役时间1924年-1958年军衔 二級上將 (追晉)部队四十七師指挥東北剿匪總司令部參謀長陸軍�...
Burt BacharachBacharach (1972)LahirBurt Freeman Bacharach(1928-05-12)12 Mei 1928Kansas City, Missouri, A.S.Meninggal8 Februari 2023(2023-02-08) (umur 94)Los Angeles, California, A.S.PekerjaanPenulis lagu, pianis, penyanyi, konduktorTahun aktif1950–2023Situs webBurt Bacharach Burt Freeman Bacharach (/ˈbækəræk/ BAK-ə-rak; 12 Mei 1928 – 8 Februari 2023) merupakan seorang pianis dan komposer berkebangsaan Amerika Serikat yang menjadi terkenal saat membuat pop hit...

Cet article est une ébauche concernant une localité du Massachusetts. Vous pouvez partager vos connaissances en l’améliorant (comment ?) selon les recommandations des projets correspondants. FoxboroughFoxborough en 2010.Nom local (en) FoxboroughGéographiePays États-UnisÉtat MassachusettsComté comté de NorfolkPartie de Massachusetts House of Representatives' 1st Bristol district (en), Massachusetts Senate's Bristol and Norfolk district (en)Superficie 54,13 km2Altitud...

Disambiguazione – Canzone popolare rimanda qui. Se stai cercando altri significati, vedi Canzone popolare (disambigua). Il canto popolare indica genericamente vari generi di musica che vanno da quelle pensate e scritte per il popolo (popular music o pop), a quelle provenienti dal popolo (musica folk). Canto di corteggiamento nella Russia del XIX secolo (stampa su tela, 1880) Al primo gruppo appartengono, quindi, la quasi totalità delle musiche che quotidianamente si possono ascolt...

Ford MondeoDescrizione generaleCostruttore Ford Tipo principaleBerlina Altre versioniStation wagon Produzionedal 1993 Sostituisce laFord Sierra SeriePrima (1993-2000)Seconda (2000-2007)Terza (2007-2014)Quarta (2014-2022)Quinta (2022-) Altre caratteristicheAltre antenateFord Taunus e Ford Cortina Della stessa famigliaFord CougarFord Fusion (America) La Ford Mondeo è un modello di autovettura appartenente al segmento D prodotta dalla casa automobilistica statunitense Ford dal 1993 e giun...

Численность населения республики по данным Росстата составляет 4 003 016[1] чел. (2024). Татарстан занимает 8-е место по численности населения среди субъектов Российской Федерации[2]. Плотность населения — 59,00 чел./км² (2024). Городское население — 76,72[3] % (20...

岸信介佐藤信介 日本第56、57任內閣總理大臣任期1957年2月25日—1960年7月19日君主昭和天皇副首相石井光次郎益谷秀次前任石橋湛山继任池田勇人 日本內閣總理大臣(臨時代理)任期1957年1月31日—1957年2月25日总理石橋湛山前任石橋湛山继任岸信介 日本防衛廳長官(臨時代理)任期1957年1月31日—1957年2月2日总理岸信介(代,兼)前任石橋湛山(代)继任小瀧彬(�...